Lifts & Elevators
Utility Elevator’s philosophy revolves around providing safe, reliable, and high-quality products that exceed elevator safety standards. We actively source products from reputable manufacturers to meet diverse customer needs. In addition to standard lifts, we provide custom-designed solutions tailored for specific applications. We guide customers in defining their vertical transportation needs and import suitable lift applications or even design and manufacture according to specifications when required.
Our product solutions for your building
When initiating a new architectural project or upgrading an existing structure, the first step in elevator design involves considering the type of building. Each setting – residential, office, commercial, hospital, and industrial – has unique requirements for functionality, speed, capacity, and durability. Understanding these distinctions helps in selecting the most suitable elevator models.
Elevator design requires meticulous attention to detail, tailored to the building’s size and purpose. Hospitals may need separate elevators for patients, staff, and visitors, while tall buildings require faster and larger elevators for smooth traffic flow. However, the elevator system is often overlooked in new developments, leading to complications requiring customization. Therefore, a careful approach to design is crucial for harmonizing passenger and goods flow within the building.
Key factors to consider for new installations or replacement installations.
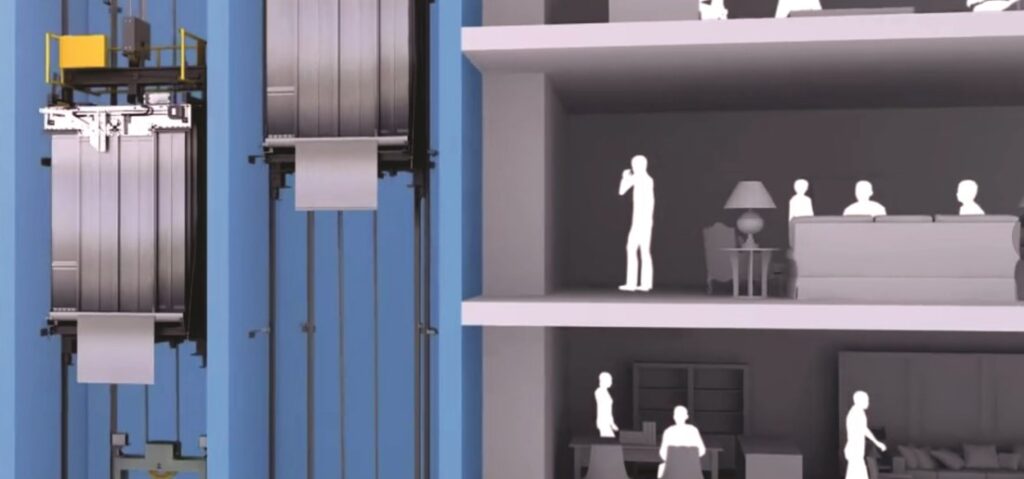
- What type of building are we dealing with, and what is the height of the building?
- How many lifts are required to deal with the building’s traffic flow?
- What cabin design will be required, considering disabled passengers, goods, and the type of doors and the orientation of the doors?
- What lift speed and load capacity are required to effectively handle the building’s vertical traffic
- What will be the most efficient lift arrangement, simplex, duplex, and installation area in the building?
- Is it an indoor or outdoor application?
- What specific technology will best suit the project’s requirements?
- What eustatic values are required?
- What regulation will be applicable? Regulation may call for a firefighter’s lift in a high-rise building.
- What drive system will suit the required application the best? Following are a few options available: –
- Traction type (Motor room and Motor room less
- Hydraulic
- Screw driven
Everything you need to know about:
Traction, Hydraulic, Screw Driven Lifts
Preliminary to installing a new lift, there is a lot to consider, as mentioned in “Key factors to consider”. We have outlined factors for consideration when planning a new elevator installation or an elevator replacement program.
We believe the primary consideration will be the drive-type system that will ultimately shape your decision.
Traction Elevators
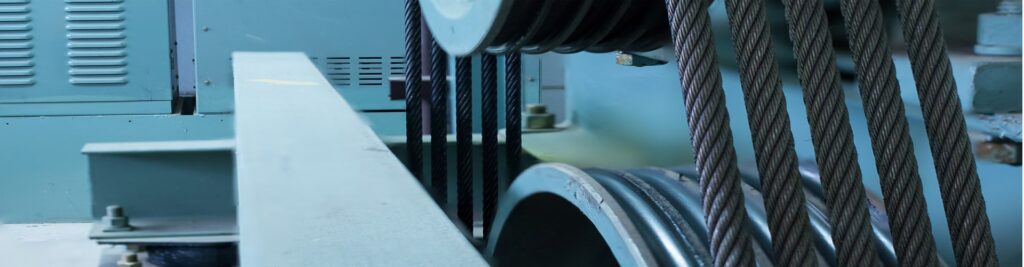
This type of elevator operates via a traction sheave attached to a motor, using steel ropes or belts and a counterweight to move the cabin up and down. There are two types of traction elevators: “Geared Traction” and “Gearless Traction”.
Traction elevators are typically more energy efficient and provide passengers with a smoother and quieter ride.
Geared traction (Machine room application)
Advantages
- Overhead or basement machine rooms.
- Less expensive installation than gearless.
- Speeds faster than hydraulic or screw-driven lifts.
- Smoother ride quality than hydraulic systems.
- Accommodates front and rear door openings.
- Non-proprietary equipment.
- Can be refurbished.
Disadvantages
- Additional space requirement as a motor room is required at the top or bottom of the shaft
- Higher maintenance
- Lower speed than Gearless traction
- Greater structural considerations because the elevator is supported at the top of the shaft
- Requires a pit normally 1 – 1.5m deep
- Extended installation time depending on the height
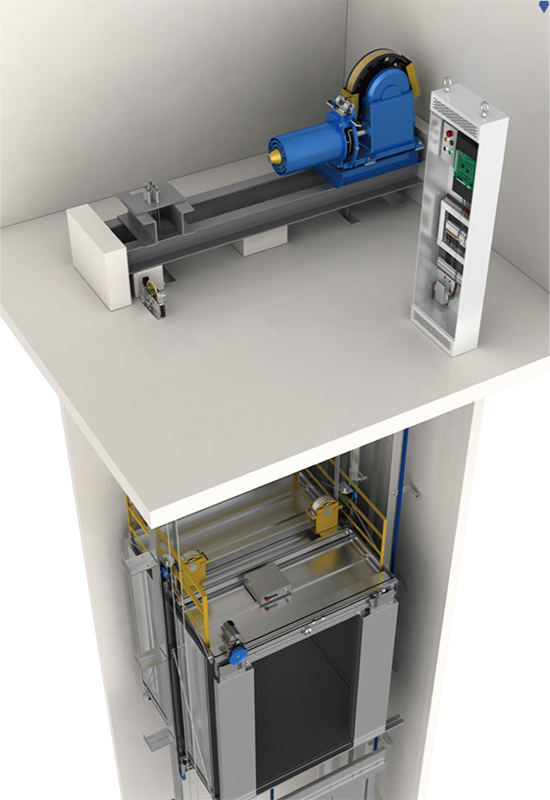
In this setup, a reduction gearbox connects to a high-speed motor, ropes, and a counterweight. The elevator car’s main guide rails are mounted on its side, with two additional guide rails for the counterweight on one side or the rear. Typically, the geared machine is situated above the shaft in a motor room. However, in some non-typical applications, the geared machine may be located at a lower landing beside the elevator shaft.
Gearless traction (Machine room and machine room less application)
Advantages
- Gearless traction provides versatility as this application can be applied in a motor room and motor roomless application.
- Gearless motor roomless applications provide space saving as the machine room is located in the shaft.
- Gearless traction increases energy efficiency and provides a smooth, quiet ride.
- Greater energy efficiency due to the Permanent Magnet AC Motor.
- Low noise level.
- Superior speed and performance to that of a typical geared traction application.
- Smoother ride quality than hydraulic systems.
- Accommodates front and rear openings (Through entrances).
- No risk of oil contamination.
- Lower maintenance cost.
- Non-proprietary equipment.
Disadvantages
- Gearless traction has a higher initial cost than geared version.
- Greater structural considerations because the elevator is supported at the top of the hoistway
- Increased overhead/pit requirements
- Can’t be refurbished (Replacement only)
- Extended installation time depending on the height
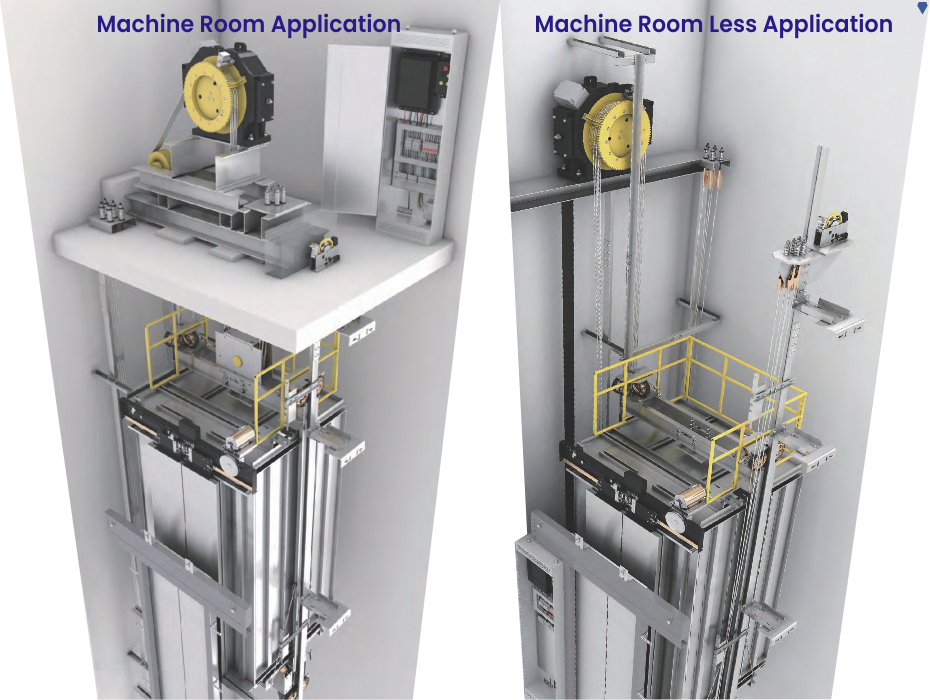
Gearless traction elevators offer a more advanced solution, directly attaching a sheave to the traction motor. The motor’s rotation directly powers the traction sheave without intermediate gearing. This configuration employs a gearless machine, ropes, and a counterweight. Main guide rails mount on the elevator car’s side, with two additional guide rails for the counterweight on one side or the rear. Typically, the gearless machine sits on the side at the top of the shaft.
Hydraulic Elevators

In hydraulic elevators, a bottom-placed piston supports the system, and the cylinder and drive modules are connected via hoses and pipes. The power unit, comprising a tank, motor, pump, and flow control valve, operates as follows: the motor drives the pump, which delivers oil to the flow control valve. This valve directs oil into the cylinder through a hydraulic hose, increasing pressure to push the piston and elevate the elevator.
During descent, the elevator lowers by gravity, with the pump and motor disengaged. Ride characteristics are regulated by the flow control valve, facilitating the return of oil from the cylinder.
Types
Hydraulic Elevators are available in single and twin-cylinder configurations, which can also be telescopic or non-telescopic.
Roped Hydraulic Elevators
(Indirect transmission). Use a combination of ropes, sheaves and a piston to move the elevator.
Travel is limited to around 18m, equivalent to a 5-6 story building. This application is the most common and preferred in South Africa.
and the preferred application in South Africa.
Hole-less Hydraulic Elevators
(Direct transmission) Similar to the conventional type, it doesn’t require a hole or sheave fixed below the pit.
Telescoping pistons allow 15 meters of travel distance; a non-telescoping piston only allows about 6 metres.
Advantages
• Hydraulic Lifts usually have a low initial cost.
• Easy installation, operation, and maintenance, as well as high durability.
• Less strain on the building structure with the advantage of transferring most of the elevator structural loads into the pit floor,
• Relative quickly to installation.
• Highly effective with heavy loads thanks to the hydraulic lifting force.
• Lower pit and overhead requirements with standard travel.
• No roof access is required.
Disadvantages
• Hydraulic elevators utilize more energy because they use an electric motor that works against gravity.
• The possibility of oil leaks exists, which requires oil top-ups.
• A defective flow control valve can cause the cabin to stop short or below floor level, which is problematic for wheelchair users.
• Oil leaks can be smelly.
• The oil capacity of a hydraulic lift is a minimum of 100 L, which increases the safety risk due to the explosive liquid factor.
• Requires a motor room at the lowest level for the tank, motor, valve system and control system.
• Low-rise application due to limited travel.
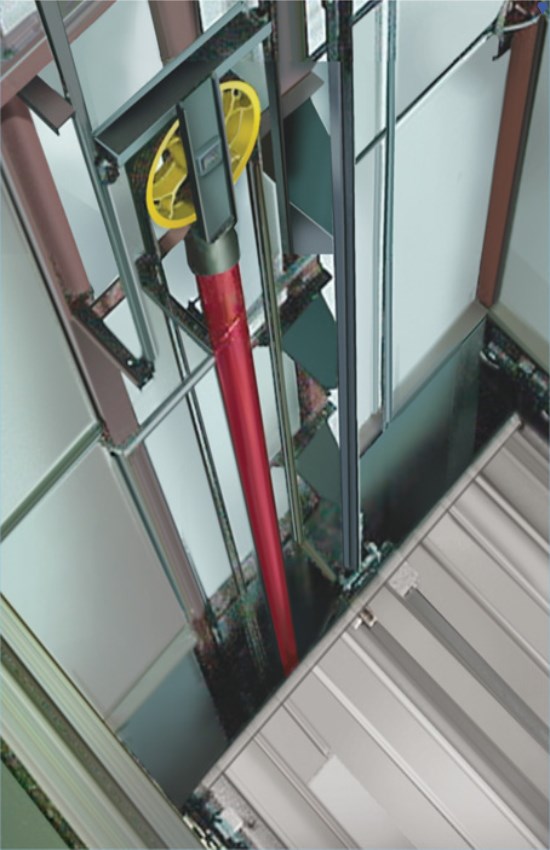
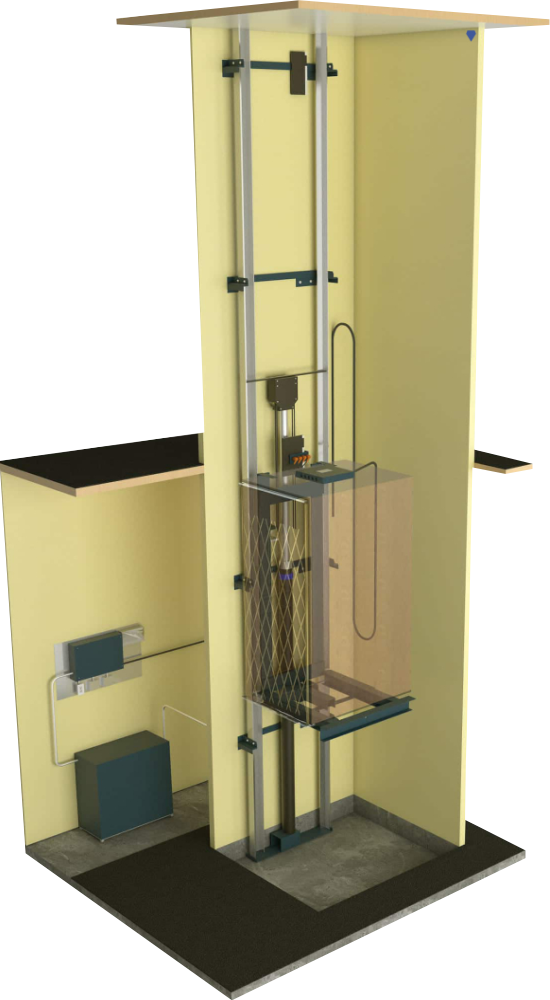
Screw drive
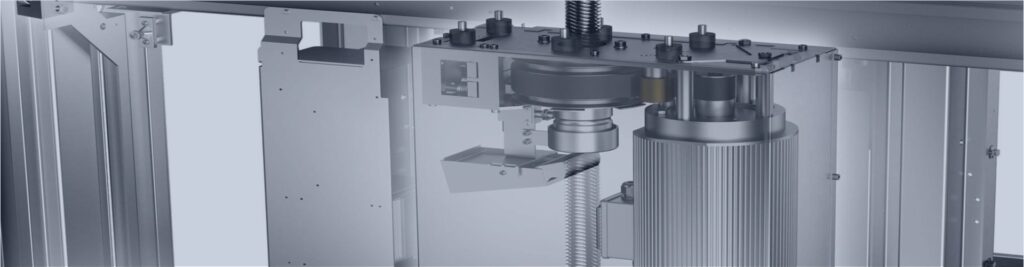
A screw-driven elevator has a simple but ingenious system for elevation: Designed on a patented screw and nut technology which drives the lift via an energy-efficient electric motor. The platform or cabin is attached to a drive nut that moves up, and down the screw.
Advantages
• The screw and nut drive is a very safe and reliable system with a long lifespan.
• Screw lifts are comparatively cost-effective.
• The drive system is also compact enough to be fitted inside the lift shaft, which is why this type of elevator requires no separate machine room,
• No extra headroom.
• Can be installed without a lift pit.
• Low maintenance cost.
• They are easy to install and usually take only 7-10 days with minimal civil work
• Indoor and outdoor installation compliant.
• Self-standing structure
Disadvantages
• Lower travelling speeds for safety reasons limited to 0.25m/s as per EU regulations.
• Weight restrictions on screw lifts compared to hydraulic or traction lifts.
• Not suitable as a goods lift in an industrial environment.
Next-generation mobility today
Choosing the correct elevator models and materials for your building’s use will help ensure your equipment’s effective performance and long-term durability while appropriately serving the users’ needs. Our range of products from various prominent, leading manufacturers of good repute will ensure the correct application for your project.
Passenger and freight elevators that will deliver:
• Increased transport capacity
• Reduced space requirements
• Enhanced safety
• Improved energy efficiency
• Latest technology
• Available customized design
Proprietary vs Non-proprietary Elevators
We believe that utilizing non-proprietary equipment is crucial for elevator owners, as it ensures availability and flexibility. With an open platform system, any qualified service provider can maintain or repair the equipment as needed.
Non-proprietary equipment eliminates the need for company-specific tools, passwords, or software, unlike proprietary control equipment. This distinction is significant as proprietary parts tie elevator owners to long-term escalating costs for product support and maintenance.
Moreover, non-proprietary options offer the same level of function and reliability without the hefty price tag and exclusivity associated with proprietary parts and software used by some manufacturers.
We understand that all the considerations can become overwhelming therefore our product experts at Utility Elevators will assist you to obtain the correct configurations and specifications to ensure your project’s success, from design and installation.
Product Centre
Our product range for transporting mainly people in your low-rise, mid-rise, and high-rise and private homes safely, efficiently, and comfortably consists of the following products:
Our product range for transporting mainly freight and goods – Lifting the weight: